Introduction
Concrete served as the foundation upon which modern construction was laid, and it has been of enormous importance due to its high strength, durability, and versatility.
Traditional concrete is, however, subjected to various problems, such as cracking, shrinkage, and brittleness under particular conditions.
Fiber reinforcement in concrete batches is a contribution made to increase the properties of concrete from both the engineers’ and researchers’ perspectives. Among these is one of the most applicable fibers, polypropylene fiber (PP fiber).
Table of Contents
PFRC is modified concrete that consists of PP fibers to enhance the structural capacity of conventional concrete.
These synthetic fibers consist of thermoplastic polymers, thereby improving the performance of concrete against cracking, impact, and shrinkage, thus being a suitable product for high-performance construction applications.
In this blog, we will discuss the properties of polypropylene fibers and the role they play in concrete, while the effects brought about by their addition to fresh and hardened concrete will also be considered, as will issues employees may experience in employing them.
Properties of Polypropylene Fibers
Polypropylene is a light synthetic fiber obtained from the propylene polymer. It has excellent mechanical and chemical properties that make it useful in concrete reinforcement. Their key characteristics include the following:
1. Physical Properties
Polypropylene fibers are among the lightest synthetic fibers, weighing around 0.91 g/cm³. They develop a very high tensile strength, which can go up to 300–700 MPa; this increases the durability of concrete under a certain stress and deformation. They have many different lengths, from 6 mm to 50 mm or so, according to the application.
2. Chemical Properties
Inert Nature: Polypropylene fibers have stable chemical characteristics; therefore, they never react with other ingredients in the concrete mixture. They remain intact and in their optimum performance, thus giving them a long service life.
Resistance to Alkalis and Acids: Unlike steel fibers, they do not rust in harsh conditions; therefore, they are preferred for marine and industrial use.
Non-Absorbent: These fibers do not absorb water and do not pose a problem of excessive water retention or expansion of the concrete mix.
3. Thermal Properties
Melting Point: The melting temperature of polypropylene fibers is approximately 165C. This is beneficial since it contributes towards stability at normal temperatures.
Thermal Conductivity: Insulation properties lead to more thermal efficiency in concrete structures. These properties make polypropylene fibers handy for reinforcing concrete in a multitude of construction applications.
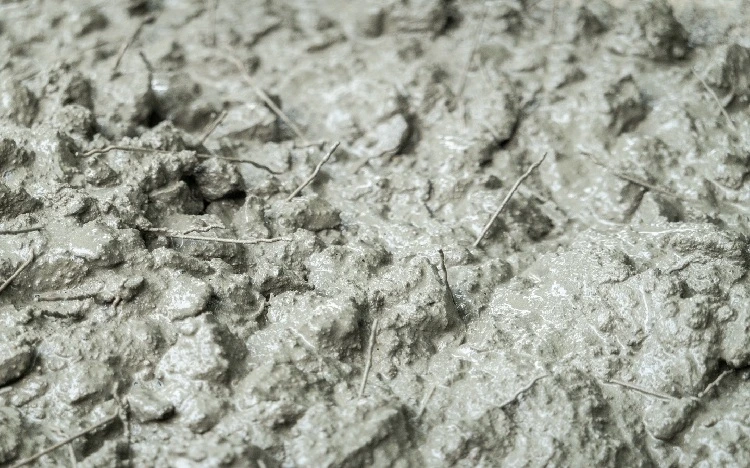
Role of Fibers in Concrete
Concrete is one of the most common construction materials because of its high compressive strength, low cost, and durability.
But alongside these advantages, concrete possesses some innate weaknesses, such as brittleness, cracking due to shrinkage and thermal stress, or mechanical loading. All these may compromise the long-term structural integrity of concrete elements.
With this in mind, the addition of polypropylene (PP) fibers to concrete can enhance the performance of not only a specific job but the whole structure by overcoming these deficiencies.
Inserting PP fibers as reinforcement works to the benefit of concrete by increasing durability, toughness, and crack resistance for multiple applications. A few methods of how fibers help improve performance for concrete are:
1. Crack Resistance and Control
Concrete cracks for various reasons: plastic shrinkage, thermal expansion, drying shrinkage, and structural loads, among others. Once a crack starts, it resonates into a much bigger crack due to load application, which conforms to the integrity of the structure.
The polypropylene fibers are dispersed uniformly around the concrete mix, forming a reinforcement matrix that controls micro-cracking, thereby acting as bridging constituents of small cracks and intercepting them prior to their increase to larger cracks.
Accordingly, this reinforces structural longevity, greatly reducing maintenance costs in concrete such as bridges, pavements, water tanks, and buildings facing extreme weather conditions.
2. Enhanced Impact Resistance
Concrete structures sustain sudden loading and impact forces that lead to damage or surface degradation.
The impact resistance of concrete is increased by polypropylene fibers as they greatly improve concrete toughness. Furthermore, the fibers absorb impact energy and distribute loads more evenly so complete failure is avoided.
This is especially good for use in industrial flooring, airport runways, earthquake-resistant structures, and military applications where cracking and shattering can occur due to dynamic and repetitive loading on the concrete.
3. Improved Flexural Strength
Though the main role of polypropylene fibers in not to boost compressive strength, their contribution toward flexural strength is appreciable. Concrete is naturally weak in tension, making it ideal for cracking during any bending or flexural loading.
The PP fibers enhance ductility and toughness, causing concrete to bend before it shatters instead of breaking with no warning.
PFRC is thus very advantageous to applications where resisting bending is crucial-such as roadways, bridge deck, tunnel linings, and precast concrete elements.
4. Durability
Polypropylene Fiber Reinforced Concrete is extensibly durable compared with conventional concrete; Polypropylene Fiber Reinforced Concrete will withstand normal environmental stressors like:
- Freeze-thaw action: This causes expansion and contraction of concrete and, subsequently, cracks.
- Water penetration: This leads to corrosion of the steel reinforcement in reinforced concrete.
- Chemical attack: It may happen that in industrial and coastal areas, the concrete may degrade.
The durability of PP fibers gives concrete a myriad of advantages, in that it lengthens the life cycle of structures and reduces the lifecycle costs for repair and maintenance in the long run, therefore constituting an economical option for marine structures, highways, and wastewater treatment plants.
5. Better Fire Resistance
One of the concrete structures’ pronounced threats includes the explosive destruction of concrete surfaces brought by high temperatures.
When heated, the water entrapped inside the concrete would vaporize to form steam; in doing so, it would create internal pressure that would cause spalling.
The polypropylene fibers work beautifully in obtaining fire resistance by melting at high temperatures, approximately 165°C, thereby creating microchannels within the concrete.
During a fire, these microchannels create pathways for moisture to the surface instead of building internal pressures that lead to explosive failure.
Therefore, PFRC remains the material of choice for fire-prone structures such as tunnels, underground metro systems, and industrial buildings with an ongoing interest in improving fire resistance and ensuring safety.
Properties of Polypropylene Fiber Reinforced Concrete
The introduction of polypropylene fibers affects the properties of both fresh and hardened concrete, thereby improving the performance of the concrete in its diverse applications.
Effects on Fresh Concrete
Polypropylene fibers, once added to fresh concrete, interfere with workability, density, cohesion, and setting time. There might need to be minor tweaking in the mix design, but the rewards outweigh the challenges.
1. Reduction in Workability
One of the greatest obstacles of PFRC is its limited workability. Polypropylene fibers do not absorb water during mixing; thus, they do not contribute to the fluidity of the mix. Instead, they increase internal friction, rendering concrete stiffer, thus cumbersome to ascertain and finish.
Such a problem can be dealt with by alterations in the mix design; for example:
The application of superplasticizers may enhance fluidity without increasing the water content of the mix.
Optimizing fiber dosage enables the reinforcement and workability balance to be achieved.
Use of better mixing techniques to assure homogeneity dispersal of fibers.
The benefits of PFRC use, despite the challenges with workability, include crack control, durability, and impact toughness-adds up to PFRC being a worthy material for all construction works.
2. Air Entrainment
The polypropylene fiber sometimes causes a slight entrapment of air bubbles in the concrete mix, which in turn affects somewhat the density and strength characteristics of the concrete.
The evolution of air in the system may cause slight reductions in compressive strength, though this is not usually significant in most applications.
Proper mixing techniques and controlled fiber addition will be adopted here to minimize the air entrapment, allowing the final concrete structure to maintain its design strength and performance.
3. Improved Cohesion
The benefits of polypropylene fiber incorporation include more excellent cohesion inside the concrete mixture. Fibers help in controlling segregation and bleeding, thus supporting a homogenous mixture. This is of particular advantage for:
Shotcrete is used in tunnel linings and slope stabilization.
Precast concrete elements, which require a constant quality and surface finish.
PFRC is able, through its greater cohesion, to form itself into stronger, more stable concrete blocks that promise longer life and serviceability.
Effects on Hardened Concrete
Polypropylene Fiber Reinforced Concrete (PFRC) is, after curing, vastly superior to conventional concrete in terms of mechanical and durability properties.
These properties mate with PFRC an apparent advantage, justifying its use in construction where crack resistance, toughness, impact strength, and durability form points of great consideration. When the concrete achieves a full set, PFRC has its specific advantages, which are listed below.
1. Reduced Cracking
One of the most remarkable aspects of the incorporation of polypropylene fibers into concrete is that they dramatically reduce problems related to plastic shrinkage cracks.
Concrete develops such cracks subject to the conditions obtained during the hydration process, particularly early when the concrete is gaining in strength. Cracks are, therefore, a result of moisture loss and the resulting formation of stresses inside the concrete.
With the help of PP fibers, a three-dimensional reinforcement network gets established in the concrete matrix. Once potential cracks start forming during early stages of hydration, they act as tiny little bridges, preventing cracks from turning into larger fractures.
Long-term stability of the concrete, with less need for excessive repair and maintenance after the fact, is the first immediate benefit.
Quite literally, the immediate intended benefit of crack-resistant concrete means that for roadways, bridges, tunnels, and water-retaining structures even small cracks could become the crux of highly serious durability issues after years.
2. Higher Impact Resistance
PFRC is superior to conventional concrete regarding impact resistance, making it a more favorable choice for buildings subjected to heavy loads, shocks, or other sudden forces.
Due to its brittle nature, traditional concrete will fracture and split an impact. On the other hand, polypropylene fibers help absorb energy and spread the force around more dispersing and efficient.
This property is very beneficial in high-traffic places, such as industrial floors, airport runways, loading docks, and bridge decks, where constant mechanical stresses can shorten the life of a structure.
PFRC resists surface chipping, spalling, and structural damage and is therefore long-lasting in these conditions.
3. Improved Toughness and Ductility
Plain concrete is brittle by nature, and sudden failure will occur based on loading and subsequent overloading. PFRC, however, will enhance the toughness and ductility of the concrete to allow it to sustain some deformation without imminent (catastrophic) failure.
After micro-cracking occurs in the concrete, it is the presence of the polypropylene fibers that holds the concrete in place, therefore enhancing its load-bearing ability after cracking.
This characteristic makes PFRC particularly effective in seismic-resilient structures. Such applications mainly include pavements and tunnel linings, where survival against dynamic loading and deformation becomes pertinent to the ground stability.
Unlike conventional concrete, which develops great cracks in the concrete under stress, fiber-reinforced concrete keeps its structural integrity even in the case of fluctuating loads.
4. Fire Resistance Enhancement
There is always the fire safety of concrete, which comes in the bigger picture nowadays, predominantly in high-rise buildings, tunnels, and industries.
Concrete undergoes spalling under violent fire conditions when surface layers explode off as vapor from trapped moisture expands rapidly. This destructive feature weakens the structure and may cause structural failure under fire conditions.
Polypropylene fibers serve as a built-in fire-resistant mechanism. The fibers melt at high temperatures, creating microchannels for the gradual escape of moisture vapor.
Thus, built-up pressure does not burst the interior of the concrete, which drastically reduces the possibility of explosive spalling. PFRC improves the fire safety of concrete structures, making them more durable when exposed to fire.
5. Resistance to Freeze-Thaw Cycles
In cold weather conditions, freeze-thaw cycles typically affect concrete structures, involving confined water in the concrete expanding on freezing and shrinking on irreversible thawing. Gradually, this leads to micro-cracking, surface scaling, and inevitable breakdown.
PFRC is remarkably resistant to freeze-thaw damage, as it controls cracks and thus limits water infiltration. Polypropylene fibers will form a network to lower the permeability so that no excessive water will enter the concrete and cause damage from repetitive cycles of freezing and thawing.
This makes PFRC an ideal construction material, as far as dams, highways, bridges, sidewalks, and airport runways are concerned, in areas with winter extremes.
Obstacles in the Use of Polypropylene Fiber Reinforced Concrete
Although PFRC entails a number of advantages, its implementations are some challenges. Engineers and construction-related professionals have to face those challenges to enhance the quality of PFRC applications. Few of the common problems in this regard include:
1. Workability Problems
Perhaps the greatest drawback of PFRC orientation is its associated workability problems. The incorporation of polypropylene fibers into the concrete mix increases the internal friction in the mix, rendering it inconvenient during handling, pouring, and finishing.
Compared to common concrete, which has good flow, fiber-reinforced concrete will generally be stiffer and not cohesive, which complicates surface finishing and achieving uniformity and smoothness.
Furthermore, they do not absorb water and, therefore, do not contribute to the fluidity of the mix. Mixing and placing other materials would be cumbersome.
This may be addressed by adding either superplasticizers or water-reducing admixtures, depending on the ease of workability, while not impacting the strength and durability of concrete in any way.
2. Higher Initial Cost
Polypropylene fibers, when used in concrete, will add to the initial construction cost. The provision of high-quality synthetic fibers becomes an additional material cost. Moreover, the specialist handling and mixing processes needed for PFRC will push up the labor cost.
However, while there is a large initial investment, it is worth considering the long-term economic benefits. Durability, resistance to cracking, and extended lifespan are inherent characteristics of PFRC; thus, less money will be spent on its repairs or maintenance.
It is these benefits that can eventually justify the initial investment, especially in large-scale applications of PFRC used for industrial flooring, pavements, and bridges.
3. Mixing Problems
Another major problem is obtaining a good fiber distribution in concrete mixtures. Polypropylene fibers do have a tendency to aggregate, so nonuniform dispersion will likely result.
But if fibers are not uniformly distributed, some parts of the structure may have no reinforcement, which would not be efficient for PFRC.
The adoption of sound mixing methods and equipment would prevent this. Mechanical fiber dispensers would assist in better fiber distribution.
The stepwise mixing process ensures that fibers are introduced gradually into the concrete mix, avoiding fiber balling and providing for an even blend.
4. Minimal Contribution to Compressive Strength
The compressive strength of PFRC does not receive considerable enhancement, which is a disadvantage. Polypropylene fibers improve toughness, ductility, and impact resistance.
On the other hand, steel fibers impart both tensile and compressive strength. Thus, PFRC does not seem suitable for structural parts requiring high compressive strength, such as columns and heavy load-bearing walls.
So, its range of usage may not be preferable in cases where compressive strength is much more significant than crack resistance, durability, and toughness itself.
Applications in this context are industrial flooring and tunnel linings and also shotcrete usage, in which they could be more beneficial because of their prevention of shrinkage cracks and durability rather than their compressive performance.
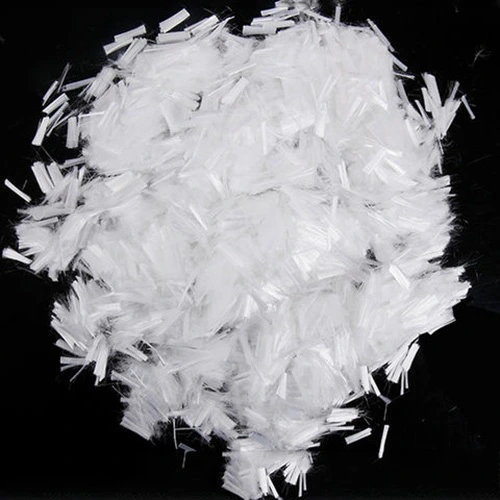
Conclusion
This development can explain the building technology which we refer to as polypropylene fiber reinforced concrete. With the aid of the lightweight, chemically stable fibers used in the concrete mixture, engineers would be able to augment the concrete with crack resistance, durability, impact strength, and fire resistance.
While there are problems in its workability and high cost, the future potential for PFRC credits the value of implementing it into future construction for reduced maintenance costs and extended lifespan of structures.
As demands in construction continue to evolve, it wouldn’t be surprising if PFRC takes the lead in building stronger, safer, and more sustainable structures around the globe.