The parameter one’s concerned with concrete is its strength, durability, and performance. By using an appropriate concrete admixture in performing residential, commercial, and industrial projects, you may ensure desired results.
Concrete admixtures provide a whole lot of benefits to achieve quality work with respect to workability, strength, etc. However, how do you choose the right concrete admixture for your needs?
What Are Concrete Admixtures?
Concrete admixtures are the materials added on-site into concrete during mixing to alter some of its properties. Additives are usually in liquid, powder, or granular form and can modify the concrete in various aspects. Such as workability, durability, observable time, and resistance to harsh environments.
What Are the Benefits of Using Concrete Admixtures?
Some of the key advantages include the following:
1. Improved Workability
Admixtures like plasticizers and superplasticizers increase the workability of concrete without providing extra water. Therefore, they facilitate placement and finishing, particularly of complicated or congested formwork, while ensuring that strength and durability remain intact.
2. Accelerated Setting and Curing
Accelerating admixtures can be added to concrete to increase setting time, particularly to deal with cold weather or extremely quick turnaround times on contracts, thereby overcoming delays and keeping on schedule.
3. Enhanced Long-Term Durability
Corrosion inhibitors or water-reducing agents can provide certain types of concrete admixtures for major improvements to the durability of concrete. As examples, corrosion inhibitors prevent embedded steel from rusting and deteriorating, while water-reducing agents aid in lowering the permeability of the concrete. Hence improving its resistance to freeze-thaw cycles and chemical exposure.
4. Enhanced Strength
Admixtures can elevate the concrete’s compressive strength to the required applications of high-strength concrete. Such minerals that are usually used as admixtures are fly ash or silica fume, which give long-term strength and control the heat of hydration in mass concrete pours.5.
5. Sustainable Benefits
As there is increasing awareness of sustainability in construction, fly ash, slag, and other recycled materials used as concrete admixtures can go a long way to reduce the carbon footprint in concrete production.
Most of these materials are by-products from other industries that also help reduce wasted material while giving performance advantages.
Factors to Consider When Choosing Concrete Admixtures
The selection of admixture for concrete work involves one of various studied factors. Here a few of such noted considerations.
1. Environmental Conditions
The local climate and environmental conditions hold much importance in determining the admissible type of admixture. For example:
Hot weather: In hot weather conditions, a retardant type or cool water may be required to enable a slower setting of concrete and keep workability time higher.
Cold weather: In cold weather, it may be advisable to utilize an accelerator type of admixture or preheat the water, guaranteeing proper hydration and faster curing times.
Exposure to aggressive chemicals: If the concrete will be exposed to harsh chemicals (e.g., in industrial environments or near the coast), then employing corrosion inhibitors or water-repellent admixtures will ensure an extended life for the structure.
2. Concrete Mix Type
Each of the projects may merit a different mixing type of concrete. It could be a lightweight concrete- one that could take either high strength or even self-compacting concrete (this type needs to be filled without vibration and compaction). The type of concrete desired will decide the specific admixture that one would use. For example:
Self-compacting concrete (SCC): Often superplasticizers are used to give the necessary fluidity and workability required to make the mix without sacrificing strength.
High-strength concrete: You may require water-reducing admixtures and mineral admixtures to improve the mix’s strength and reduce the amount of cement used.
3. Setting Time Requirements
For some projects, the time available for placing and finishing concrete is too short. If faster setting times are desired, as in the case of road repairs, then accelerators can be a big help. Retarders, on the contrary, help prolong the setting time in hot conditions, for instance, or allow for more time for placement and finishing of the concrete.
4. Workability and Flowability
Concrete workability is crucial if the concrete is to be inserted into narrow forms or at very long distances from the place of operation (which is done by pumping concrete).
Superplasticizers enhance workability without affecting strength; hence, they are best for pumping concrete or working in highly reinforced structures. The addition of viscosity-modifying admixtures also can affect the flowability of the mix.
5. Cost Considerations
The overall to very restricted budget also dictates which kind of admixtures to be used. Being a high-tech admixture in itself, such as superplasticizers or silica fume, it is likely that, although it could cost a little on the higher side, it will save money in some repair and the care for it could be reduced because of its possible durability.
Cost-effectiveness is to be examined not only in terms of the initial material cost but also concerning the long-term benefits acquired by good selection of the admixture.
6. Regulatory Requirements
Because of strict regulatory specifications or certifications, some projects, particularly in commercial or public construction, can require the use of certain types of admixtures.
It is very important to contact local building codes and construction regulation guidelines and follow all the standards and specifications set forth.
Types of Concrete Admixtures and Their Functions
The most commonly used concrete admixtures and their mechanisms are presented as follows:
1. Water-Reducing Admixtures
These admixtures decrease the amount of water for a given mix of concrete, leaving it more durable and stronger. Superplasticizers are often used for the attainment of high workability, without jeopardizing the strength of concrete mixes.
2. Plasticizers
Plasticizers are effective in increasing the workability of concrete, making mixing and placing very easy. They come in handy when concrete is to be poured into close forms with little vibration or whenever a pump is being used.
3. Accelerating Admixtures
Accelerating admixtures quicken the time for the hydration of concrete and shorten its setting time. These are especially useful when it is cold or when rapid setting is required in order to take care of fast-track construction.
4. Retarding Admixtures
Retarders can prolong the setting time of concrete, which is useful under hot weather conditions. They provide more working time for mixing, transporting, and placing concrete before it sets, thereby minimizing the risk of setting prematurely.
5. Air-Entraining Admixtures
Air-entraining agents are responsible for the introduction of tiny air pockets into the concrete mix, hence improving resistance to freeze and thaw cycles, as well as workability. They are most commonly used in regions that experience exceptionally cold winters.
6. Corrosion Inhibitors
Corrosion inhibitors protect the steel reinforcement embedded in concrete from corrosion, such as under isolation in aggressive environments like marine structures or roadways treated with de-icing salts.
7. Shrinkage-Reducing Admixtures
These admixtures reduce the shrinkage that occurs during curing, thereby reducing the potential for cracks due to drying shrinkage. This is particularly important in the case of large slabs or pavements.
8. Mineral Additives
Mineral admixtures such as fly ash, slag, and silica fume are generally used for enhancing both the strength and durability of concrete. These materials are principally by-products from other industries and provide benefits such as reduced heat of hydration and improved resistance to chemical attacks.
Importance of Quality Control in Admixture Manufacturing
Reasons quality control is important are as follows:
Consistency: It should provide a particular performance, created with concrete admixture, always. They may change in composition, quality, or character, and such an alteration may lead to a change in the properties of concrete produced with the admixture.
Safety: Some admixtures are harmful to human health if not formulated correctly. It is critical to show that the admixture is safe and meets various state and federal environmental standards within the provided limits, or if it complies with the legal requirements in effect in the area of use.
Performance Testing: Quality control controls that such admixtures reach performance levels which are required for selected applications like: Better workability, durability, or fast setting time.
Batch Testing: Admixtures before large usage should have effective batch tests which check their compatibility with other materials in the mix and show their effectiveness in practical conditions.
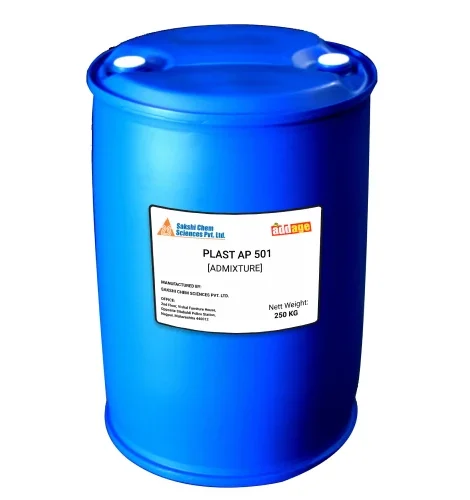
Conclusion
It is very important to choose the right concrete admixture in order to meet the performance, durability, and economy needed for your project.
Understanding just what the needs of the project are—to enhance workability, accelerate curing, increase strength, or minimize shrinkage.
This allows one to select the correct admixture that fulfills that need. To be considered are: the environmental conditions, type of concrete mix, and required setting time.