Concrete pumping is a key aspect of modern construction. It helps in faster, easier, and less labor-intensive placement of concrete, although not all concrete mixes lend themselves well to pumping.
Some might jam into the pipeline, resulting in an inconsistent flow and perhaps delays that could cost money. Pumpability is the ease with which concrete passes through the pump and pipeline systems without becoming obstructed.
Table of Contents
Knowledge of these and other parameters that can affect concrete pumpability is necessary for smooth construction operations.
This blog will cover factors affecting concrete pumpability and explain the way in which these aspects impact the effectiveness of concrete pumping using very simple terminology.
1. Concrete Mix Design
At the core of pumpability would be the way in which concrete is mixed. Various components operating together can exert varying degrees of control over the pumping of concrete.
a) Water-Cement-Ratio
The water-cement ratio affects the workability (consistency) of the mix. Too much water makes the concrete more fluid and susceptible to segregation (separation of aggregates and cement), while too little makes it too thick and viscous for effective pumpability.
Cohesive concrete with good workability can be achieved with a properly balanced water-cement ratio. The normal water-cement ratio ranges between 0.4 and 0.6, which general consideration is based on specific needs in construction.
A high ratio offers good workability, while a low ratio provides high strength. A compromise between these two opposing needs constitutes a key to seamless pumping without sacrificing the ultimate strength of the structure.
b) Aggregate Size and Shape
Collectively, the measured quantities of sand, gravel, and crushed stone form the bulk of concrete. Form, size, and gradation of the aggregate directly affect pumpability.
Aggregate that has been well-graded (with a mix of sizes) will improve flow and decrease congestion.
Round aggregates, as opposed to the angular aggregates, are easier for the pumping operation because they slide past each other much easily.
Too many large aggregates can cause blockages in narrow pipes.
Proper grading allows particles to interlock without hindrance in motion and reduces pipe friction. There must also be clean aggregates free from excessive dust and contamination, which would produce variations in mix behavior.
c) Cement Content
Cement content is responsible for the pumpability. The more the cement, the more pumpable it is, since cement, acts as a lubricant in the mix. However, excessive addition of cement can create a very sticky mix, thus increasing friction in the pipeline.
Care must be taken to proportion cement content to produce a balance between strength and workability.
An increase in cement improves the mixture cohesion and minimizes the possibility of bleeding, that is, water raising up to the surface, which could in turn weaken the final structure. However, cement in too large amounts does bear too great a cost and the problem of cracking might surface.
d) Use of Admixtures
The admixtures are specific chemicals added to concrete to improve its characteristics.
Superplasticizers enhance flowability without adding excess water. Air-entraining agents are used to loosen the concrete, hence increasing its pumpability.
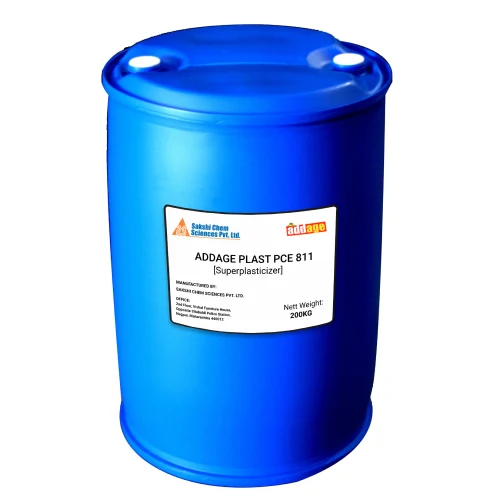

Retarders are used to slow down the setting time, therefore its use is advocated in the long-distance pumping process.
Admixtures play an important role in modern construction by allowing a finer control over the behavior of concrete. They help in the counterattack against environmental effects like extreme heats and cold weathers and safeguard uniform pumpability.
2. Concrete Pump Primer
Before pumping, a concrete pump primer is often used to coat the inside of the pipeline. This helps reduce friction between the concrete and the pipe walls, preventing blockages.
Why Is Concrete Pump Primer Important?
It lubricates the pipeline to provide a smooth flow of concrete. It prevents the loss of cement paste, which can cause blockages. It reduces the pump pressure, making the pumping process more energy-efficient.
Using a quality concrete pump primer ensures that the first batch of concrete runs smoothly, thus reducing wear and tear on the pump and pipes.
Nevertheless, it is a question of personal preference when it comes to primers as each type of activity and application of concrete accommodates different types of primers.
Certain types of primers contain polymers, retardants, or bentonite clay to create a slippery inner surface in pipes and make it easier to pump the concrete faster.


3. Pipeline and Equipment Factors
One of the factors affecting concrete pumpability by the type of pump, the layout of the pipeline, and the maintenance of the equipment.
a) Pump Type
The types of concrete pumps are divided generally into two:
Boom Pumps-Used for bulk applications, these pumps are provided with hydraulic arms. The arms are used to place the concrete in very high places or at long distances.
Line Pumps-Used for smaller applications, rigged by hand manipulating flexible hoses.
The choice of the pump must be suited to the requirements of the project to avoid creating excess pressure and possibly blockages in the lines. Boom pumps work adequately for high-rise buildings, whereas line pumps are better suited for jobs on the ground surface.
b) Pipe Diameter and Length
Wider pipes allow easy passage of concrete. Longer pipes increase resistance and require pump pressure to be increased. Bends and elbows slow down the flow of concrete in the pipeline and increase blockages.
Minimal or no sharp bends and choosing the right pipe diameter helps ensure smooth pumping and reduces wear and tear on the pumps.
c) Pipeline Cleanliness
Any dried concrete remaining in the pipes will obstruct flow. Regular cleanings are recommended to ensure a free passage of concrete.
Proper pipeline maintenance consists of daily clean outs, checks for blockages, and making sure all connections are tight so that leaks or failures do not occur.
4. Environmental and Site Conditions
External factors affecting concrete pumpability are weather and site conditions.
a) Temperature
Hot weather causes the concrete to set quickly, making it very difficult for pumping.
Cold weather slows the setting, but this may make the mix too stiff to pump efficiently.
b) Humidity and Wind
High winds and low humidity can dry out concrete, making it less pumpable.
Minimizing exposure to air and regulating water cannot but help holding fillables for pumping.
c) Altitude
Concrete loses moisture at great heights, owing to decreasing air pressure; therefore, the proper mix is required.
Water content and dosage increases/decreases depending on weather, environmental conditions, and temperature to keep concrete workable throughout long-distance pumping.
5. The Skills of the Pump Operator
The skilled approach in the control of preventing blockage by a pump operator provides for troubleshooting and smooth flow of concrete.
Why Operator Skills are Important
Modifies pump pressure based on mix types and condition inside the pipeline. Monitors the consistency of the flow to avoid segregation or blocking. Provides for continuously checking of equipment for breakdowns.
An experienced operator can quickly diagnose a problem and push on with efficient pumping. Training and good safety protocols minimize the risk of pump failures and expensive mistakes.
6. Transportation and Handling of Concrete
Concrete’s being carried up to a point for pumping has a lot to do with the efforts of a concrete pump operator, in maintaining its physical state and the rate of pumping.
Mixing time and transit: Long transportation times lead to moisture evaporation and make the mix stiffer and more difficult to pump.
Proper timing of batching and transit can help to keep concrete free-flowing.
b) Handling and storing happenings include methods of proper storing materials away from weather conditions to maintain mixing quality.
Conclusion
Understanding factors that affect the ability to pump concrete is of utmost importance to efficient construction.
It is mainly the right mix design, the correct use of the concrete pump primer, properly maintained equipment, and an experienced operator that ensure smooth concrete pumping.
In controlling the above factors, construction teams will be able to avoid costly delays or waste of materials while ensuring a quality placement of concrete.
If you’re involved in a small residential project or big commercial buildings, paying attention to these details will keep your concrete moving smoothly and efficiently.