Do you ever notice how cracks appear in your concrete driveway or sidewalk? Well, this is a very common problem, and an answer has been found – fiber reinforced concrete (FRC). Fibers such as steel, glass, or synthetic materials are woven into the concrete to make it stronger, tougher, and more durable.
Table of Contents
Now, FRC gives the concrete greater resistance to cracking, absorption of impact, and long-term exposure to conditions. Be it roads, bridges, or floors, FRC can ensure your structure will withstand the test of time. So, let’s dive into why this concrete upgrade is turning into a game-changer in construction!
Primary Effects of Fibers in Concrete
The incorporation of fibers changes the mechanical and durability properties of concrete in a transformative manner. The following sections give an overview of the most important effects:
1. Reduction in Cracking
Reduced cracking is among the significant influences of fibers within concrete, a reduction often arising from cracking formed due to either shrinkage or temperature fluctuations/mechanical stress.
This acts by fortifying the matrix of the concrete, therefore helping in the reinforcement of concrete where cracks have appeared as these fibers prevent such cracks from running further by simply bridging it. Such reinforces aesthetic quality, plus durability of concrete.
Related Post: Essential Tips to Preventing Concrete Cracks
2. Ductility and Improved Toughness
The ductility of a material implies the capacity of the material to undergo substantial deformation before rupture, while toughness indicates the capacity with which the material absorbs energy and resists cracking.
Concrete becomes ductile and tough under the influence of fiber reinforcement. This characteristic is especially significant in structures attached to dynamic loads; for example, bridges, pavements, and industrial floors demand such properties.
3. Increased Load-Carrying Capacity
Fiber reinforced concrete exhibits an increased capacity to resist loads applied to it after cracking. Unlike conventional concrete, which becomes enormously weaker with cracking, FRC performs quite competently due to the bonding effects of the fibers holding the concrete together. This property is particularly applicable to slabs, pavements, and other elements that experience high tensile stresses.
4. Explosion and Fire Resistance
Special types of fibres, synthetic microfibres, improve the explosion resistance of concrete from spalling by explosive events at fire. Such fibres will melt and produce holes in steam and gases hence preventing the sudden cracking of the concrete.
Such FRC reduces the risks during fire events where structures such as tunnels, skyscrapers and industrial buildings would be affected by fire hazards.
5. Reduced Permeability
Fibers lower the permeability of concrete so that substances, such as chlorides or water, can penetrate the matrix, causing potential harm. The applications are specifically to be noted for marine exposures and freeze-thaw cycles wherein penetration of water will cause the material to severely degrade.
Thus, fiber-reinforced concrete provides improved strength, durability, and longevity in the concrete in the aforementioned types of exposures.
6. Compatibility with Superplasticizers
Although the addition of fibers into the concrete formulations decreases the workability of concrete mixtures, it is possible to achieve a cohesive and workable mix, without loss of strength, by using superplasticizers, which are chemical admixtures that enhance flowability.
Thus these properties make FRC rather an important material in modern construction since a performance improvement is not the only advantage but also the life cycle of concrete structures.
Understanding the Necessity of Fiber Reinforced Concrete
The usage of Fiber Reinforced Concrete has evolved out of the very high demand for better and more versatile materials for construction. Home use has increased due to the following factors:
1. High Level of Durability and Longevity
Very high/lively durability as compared to conventional concrete is offered by FRC. The fibers counteract the usual shrinkage and cracking problems in concrete structures. Most importantly, freeze-thaw and chemical reaction damage resistance is enhanced, thus increasing the effective life of the structures.
2. Increased Structural Integrity
The fibers distributed throughout the concrete help in distributing stresses evenly, making the concrete less likely to crack under load.
This increases the overall strength of the concrete and improves the load-carrying ability over time. Pavements, floors, bridges, etc., benefit by way of increased load bearing and impact resistance.
3. Affordability
The very small higher initial cost of Fiber Reinforced Concrete over normal concrete is more than offset by the savings in repairs and maintenance that are realized as time progresses. Because of its durability, less frequent repair work is required for FRC structures, reducing the overall life cycle cost of the structure.
4. Enhanced Crack Control
Fiber Reinforced Concrete is mainly used in construction due to its feature of reducing and controlling cracking. Cracks are inherent in concrete through drying shrinkage, thermal expansion and contraction, and stress-induced cracking.
The fibers in FRC are arranged in such a way that cracks are bridged to inhibit their propagation; hence, it improves the integrity of the concrete structure with time. As such FRC breeds crucials of customer bases with fold structure centered on centred basic construction.
Related Post: What is the Best Way to Fix a Concrete Shrinkage?
5. Environmental Impact
The FRC promotes sustainable constructions. Increased durability of the material meant less requirement for repairs and replacements, thus reducing waste production over long periods. Also, such structures typically need less steel reinforcement, thus minimizing the environmental load due to steel production and transport.
Top Advantages of Fiber Reinforced Concrete
The advantages offered by Fiber Reinforced Concrete make it a necessary material in today’s constructions. Some of the major benefits are listed below:
1. Increased Durability and Decreased Maintenance
FRC significantly increases the resistance of concrete to cracking, abrasions, and chemical degradation, thus improving its durability. This will eventually lead to decreased maintenance costs and an increased service life for such structures.
It is very suitable for high-traffic areas, industrial floors, and pavements exposed to harsh weather conditions or chemical attacks.
2. Increase in Load-Bearing Capacity
Compared with plain concrete, FRC has considerably higher strength, primarily in tension. Thus, it is suitable for pavements, bridges, and airport runways that are going to be subject to heavy loads from various sources.
The fibers act as internal reinforcements of the concrete, thereby improving the overall load-carrying capacity and minimizing the possibility of cracking under stresses.
3. Improved Impact Resistance
An impact-resistant concrete reinforced with fibers is ideal for applications exposed to shocks or physical damage, such as industrial floors, tunnel linings, or precast elements, thus offering higher performance in terms of toughness and wear resistance by Fiber Reinforced Concrete.
4. Reduced Requirement of Steel Reinforcement
This use of natural fibers reduces the requirement of conventional steel reinforcement which means less material costs and simplicity in the construction process.
Fibers could save not only material but also considerable labour costs since, with the fiber, conventional steel reinforcement is partially replaced by synthetic fibers offering an alternative for some types of steel reinforcements.
5. Increased Fire Resistance
The fire resistance in FRC is greatly enhanced as it can serve as a thermal barrier through fiber inclusion. Synthetic fibers melt when subjected to high temperatures, preventing explosive spalling formation in the concrete. Thus, Fiber Reinforced Concrete is the perfect choice for such buildings and structures subject to fire hazards.
Key Factors Influencing the Properties of Fiber Reinforced Concrete
Numerous factors influence the performance of Fiber Reinforced Concrete, design, and application of it into consideration.
1. Type of Fiber Used
Effective by and large fiber type influences the overall performance of FRC. Steel fibers have high tensile strength and are very good for applications in which a high load has to be supported without breaking.
Synthetic fibers, such as polypropylene, prove excellent in corrosion and are very suitable for other extreme environmental applications. Some other fibers, such as glass or natural ones, are selected for certain properties, including tensile strength, thermal resistance, and value for money.
2. Aspect Ratio
Aspect Ratios are defined as ratios between the length of the fibers to their diameters. A higher aspect ratio brings about better interaction or bonding between the fibers and the concrete matrix, which brings about improved strength and toughness.
The disadvantage of very long fibers is that they are hard to mix and there will be poor workability in the concrete. Therefore, the aspect ratio should be appropriately selected according to the application requirements.
3. Fibre Volume
The fiber addition to the concrete mix affects directly the mechanical properties of the concrete. It is very common; higher fiber content proportionately provides greater strength and toughness or crack resistance.
However, in some cases, high fiber content can cause segregation, poor workability, and clumping. The inclusion of steel fiber in the concrete composition is usually limited to 2% by the total volume.
4. Mixing and Workability
It is the process through which Fiber Reinforced Concrete is mixed to achieve better homogeneity and uniform dispersal of fibers in the mix. It must do so without segregation, which would lead to improper distribution of fibers.
The type and quantity of fibers in the mix, as well as the water-cement ratio and the use of admixtures such as superplasticizers for enhancing flowability, affect the workability of FRC.
Various Different Types of Fiber Reinforced Concrete
Fiber Reinforced Concrete is complete, depending on the origin of the fibers used; steel, synthetic, glass, and natural seem to be the most popular fiber materials, each with unique advantages.
1. Steel Fiber Reinforced Concrete
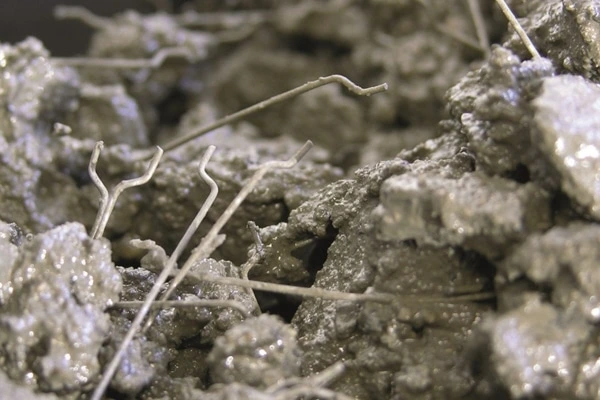
Steel fibers are probably the best-known and most-used types of fiber reinforcement. Steel fiber can be very beneficial for concrete’s performance concerning resistance to cracking, impact, fatigue, and bending.
It endows great durability and strength, making it most appropriate for heavy-duty applications like industrial floors, tunnels, and precast elements. Types of steel fiber include cold-drawn wire, cut sheets, and melt-extracted fibers. The steel fiber type will be specified according to the application and properties needed.
2. Synthetic Fiber Reinforced Concrete
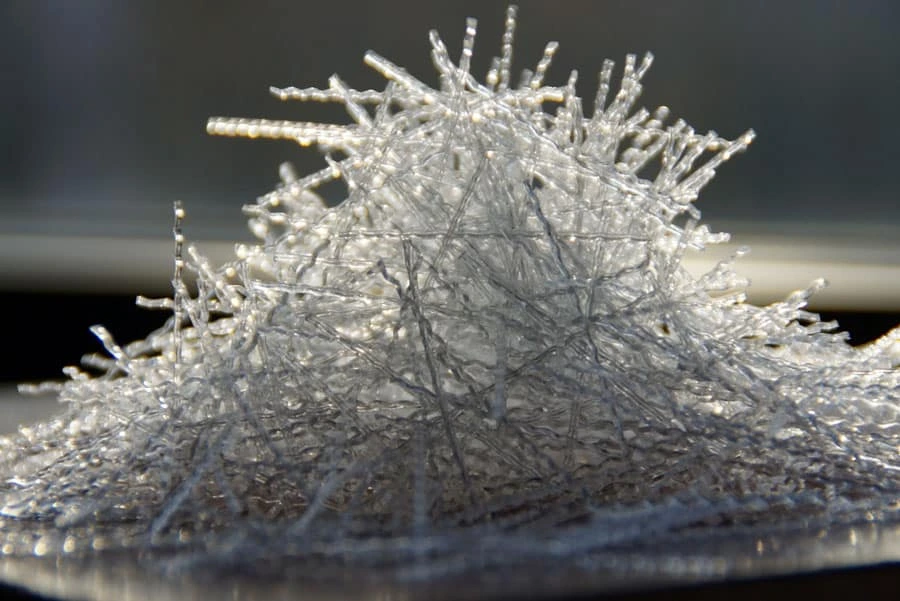
Synthetic fibers, such as polypropylene and nylon, have found their utilization in improving the performance of concrete. Their primary use is during early curing conditions, controlling plastic shrinkage cracks.
They are also not corroded, unlike steel fibers; therefore, they are significantly used in locations where corrosion or deterioration occurs. They are also very lightweight and easy to use, providing practicality on-site.
3. Glass Fiber Reinforced Concrete (GFRC)
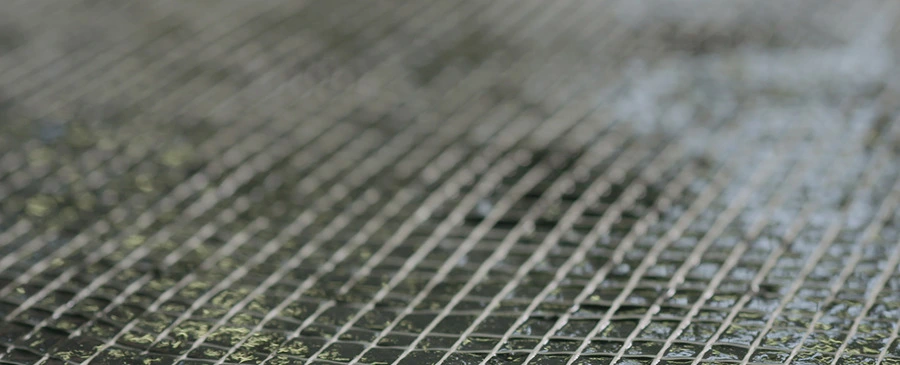
GFRC is a mixture in which the primary components include cement, fine aggregates, water, and glass fibers. It has seen wide application in thin, lightweight architectural panels, and sculptures, as well as in facades.
GFRC imparts high strength, good resilience to cracking, and applications that can afford nonstructural as well as aesthetic. Glass fibers are not as strong as steel fiber, but they do give very good durability as well as fire resistance.
4. Natural Fiber Reinforced Concrete
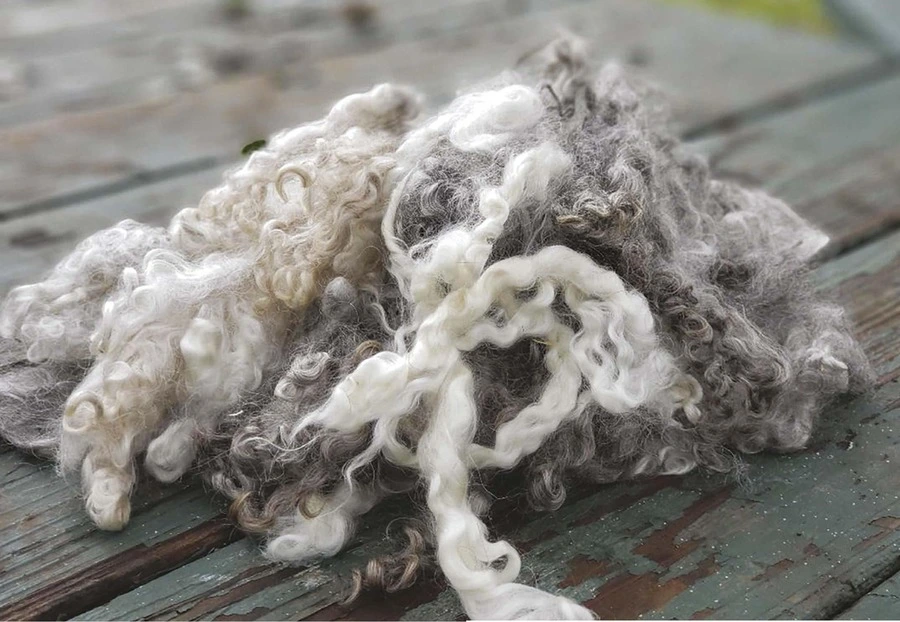
Natural fibers like those from plant or animal sources have been in use traditionally by different cultures to improve the properties of construction materials. Natural fibers are inexpensive, biodegradable, and area-available options for sustainable reinforcement of concrete in developing areas.
Some of the natural fibers for reinforcing concrete include jute, hemp, and sisal, all of which enhance the tensile strength and crack resistance of concrete.
Conclusion
Fiber Reinforced Concrete is a major revolution in construction materials. These are potentials in preventing cracking, increasing durability, and applying to various applications, which would make FRC the first choice for modern construction.
Additionally, with superplasticizers, fiber reinforced concrete represents the most superior and extraordinary opportunity in building practice. In projects for highways, industrial flooring, or houses, Fiber Reinforced Concrete has all the dependability and performance necessary for long-term success.
FAQS
What is fiber reinforced concrete?
It is a composite material that is produced from adding fiber’s like steel, polypropylene, glass, or natural fibers into conventional concrete. These fibers enhance tensile strength, crack resistance, and durability making fiber-reinforced concrete suited for structural conditions with stress or severe environment.
What is the difference between RCC and FRC?
Strength in Reinforced Cement Concrete(RCC) is provided by the placement of steel reinforcement bars (rebars), while Fiber Reinforced Concrete internalizes the reinforcement by infusion via the concrete matrix. Unlike RCC, whose effectiveness is focused on discrete areas, the efficacy of FRC is supposed to show all the levels of its performance improvement and efficiency throughout the material.
What are the major advantages of fiber reinforced concrete?
Fiber reinforced concrete has multiple advantages which include improved tensile strength, reduced cracking, better impact resistance, and greater durability. It reduces the maintenance cost as well as enhances the performance of structures with special importance for heavy-duty and industrial applications.
What are the characteristics of fiber reinforced concrete?
Fiber reinforced concrete is known for its exceptional tensile strength, crack resistance, lower permeability, and superior impact resistance and toughness. It is more durable to the environmental stresses, besides exhibiting shrinkage-related cracking resistance.
What are the advantages and disadvantages of fiber reinforced concrete?
These are some of the advantages of FRC: durability, resistance to cracking, improvement in tensile properties, and some savings in costs over time. Some disadvantages include reduced workability, higher initial costs, and fibrosis separation if improperly mixed.
What is the main purpose of fiber reinforcement in concrete?
The main purposes of fiber reinforcement in concrete are to improve tensile strength, control shrinkage cracking, and thus contribute more to overall durability under adverse construction conditions.
Why use fiber reinforced concrete?
The purpose of using fiber reinforced concrete in the construction field addresses some inherent disadvantages of normal concrete, such as low tension strength and cracks. It promises improved longevity of structures like buildings, bridges, and pavements.
Why is fiber reinforced concrete important in modern construction?
Modern construction relies on fiber-reinforced concrete because it provides solutions to such significant problems as crack formation, durability, and tensile strength in the structures. Therefore, it is often used in infrastructure projects that will last long and have the property of being high strength.
Which fiber type works best for concrete reinforcement?
Steel fibers are generally ideal for application under heavy loads, such as on industrial floors and pavements, while polypropylene works more satisfactorily in controlling shrinkage cracks. The best fiber depends on project-specific requirements and environmental conditions.
What do you mean by high-performance concrete?
High-performance concrete is a term used to describe a specific type of concrete mix which is designed to have properties such as high strength, reduced permeability, and greater durability. It usually consists of fibers and additives to improve its performance, especially under extreme conditions.
What are the functions of fiber-reinforced concrete?
The structure strengthens itself through tensile improvement, crack control, impact and abrasion resistance, reduced maintenance requirements, and extended lifespan.
What is the complete Full form of FRC?
The full form of FRC is Fiber Reinforced Concrete; it is composite material engineered with a specific function to improve tensile strength, reduce cracks, and increase durability using fibers.
What is the most significant objective of using fiber reinforced concrete?
The principal objective of using fiber reinforced concrete lies in improving the intrinsic mechanical properties of concrete over its conventional limitations, making it tougher, increasing its tensile strength, and enhancing resistance towards environmental stresses.